Data Analytics That Delivers
Real ROI

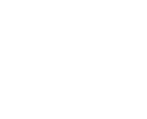



Our approach to data analytics goes deeper than standard consulting practices, combining PhD-level expertise with hands-on leadership experience from Australia’s largest resource companies to deliver real financial outcomes

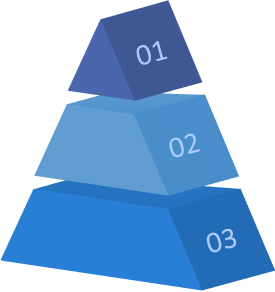
Step 1 – Engagement of Resources/consultants
Management develops a vision to use Data Analytics and AI based process improvement
Step 02 – Visual Dashboards creation
There are several dashboards created with number of charts
Step 03 – Basic trends and Comparisons
Initial Analytics to understand data behavior.


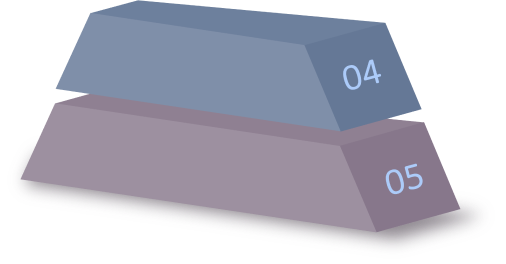
Step 4: Deep Data Fusion
Advanced analytics for deeper insights. Such as Fourier Transforms of Harmonics, Hydrocarbon decay and equipment predictive failure
Step 5: Process Optimization and corporate change
Redesign, back-test, and implement for major savings. Also implement organizational change and vision

Deep Science Approach
Our consultants extensively explore the underlying physics of challenges, focusing on areas like:
- Hydrocarbon analysis
- Vibration pattern recognition
- Reliability engineering
- Root cause analysis
- Process mining
- Preventive maintenance optimization
AI-Powered Insights with Operational Implementation
Our team doesn’t just analyze data—we’ve implemented these solutions at major resource companies.
We apply AI to:
- Uncover hidden cost savings opportunities
- Predict maintenance needs before failures occur
- Optimize resource allocation in real-time
- Transform insights into standardized procedures
- Create sustainable operational improvements
- Measure and verify ongoing value delivery
Real Results with Data Analytics
Discover how our operationalized analytics approach has delivered measurable savings for leading industrial operations
Global Mining Corporation
Analysis of 250,000 weekly labor hours revealed significant cost leakage, with 152,000 hours being unused across operations.
15% yearly savings identified
$60M annual cost reduction
16% immediate implementation savings
Industrial Equipment Operator
Material unavailability-driven reschedules created $16 million annual inefficiency cost across operations.
38% improvement in material accuracy
68% reduction in reschedule events
$11M annual savings achieved
Heavy Equipment Fleet
Large machine portfolios faced risks of major engine failures due to inconsistent lubrication standards and monitoring.
94% accuracy in failure prediction
27% extended equipment lifecycle
$8.2M saved in prevented failures
Comprehensive data analytics services designed specifically for industrial and mining operations
A team of specialists combining industrial expertise with advanced data science
Advanced Mechanix’s Data Analytics team is led by PhDs who have held leadership positions at some of Australia’s largest resource companies:
- Executive Leadership Experience – Our experts have implemented analytics solutions at scale in major mining and resource operations, managing multi-million dollar transformation initiatives that delivered substantial ROI
- Industrial Engineering – Deep understanding of mining, manufacturing, and industrial processes honed through years of on-site implementation across diverse operational environments
- Applied Data Science – PhD-level expertise in advanced statistical modeling and machine learning techniques with real-world application in resource industry settings
- Operational Implementation – Proven track record of transforming analytical insights into standardized operational practices that deliver sustained value
We don’t just theorize about solutions—we’ve actually implemented them and managed the organizational change required to make them successful. This ensures our insights are not only technically sound but also practical and immediately applicable to your operations.
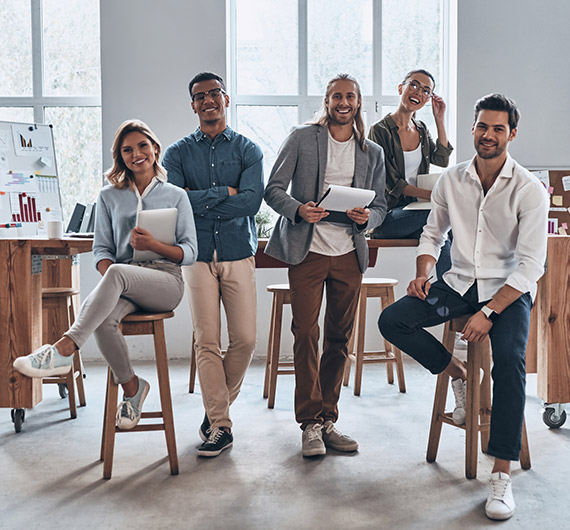
Beyond Theory
Delivering actionable intelligence that creates real operational improvements
We’ve built our reputation on delivering actionable intelligence that goes beyond theoretical analysis to create real operational improvements. Our team understands that the true test of any analytics solution is its successful implementation into daily operations.
The Operationalization Difference
Transforming insights into sustainable operational practices
What sets us apart is our focus on operationalizing analytical insights—taking them from dashboard to daily practice, then continuously enhancing and optimizing them over time. This complete lifecycle approach is why our clients achieve such substantial and sustainable savings.
Having led these transformations ourselves in leadership roles at major resource companies, we understand the practical challenges of implementation and how to overcome them.
Take the Next Step
Transform your data into measurable operational savings
Our team of PhD experts can help you identify opportunities to optimize your operations through deep data fusion and AI-driven analysis. Schedule a free, no-obligation consultation to discuss how our proven approach can be applied to your specific challenges.
Trusted by leading mining and industrial operations worldwide
Clients have achieved $140M+ in annual savings through our approach